Die mit dem Kundenauftrag einhergehende Herausforderung bestand darin, einen Halter zu entwickeln, welcher zwei verschiedene Elektromotorenvarianten für den Test eines Modellfahrzeugherstellers aufnehmen kann. Wir erhielten das Paket mit der „Hardware“ in Form der betreffenden Motoren sowie dem entsprechenden Fahrzeug. Mit dem Konstruktionsteam modellierten wir kurzerhand grobe Modelle beider Antriebseinheiten sowie wichtige Schnittstellen des Fahrzeugs. Da wir uns nur auf wesentliche Parameter (Wälzkreise der Verzahnung und Verschraubungspunkte) konzentrierten, waren wir nach kurzer Zeit bereit, den erforderlichen Motorbock zu entwerfen.
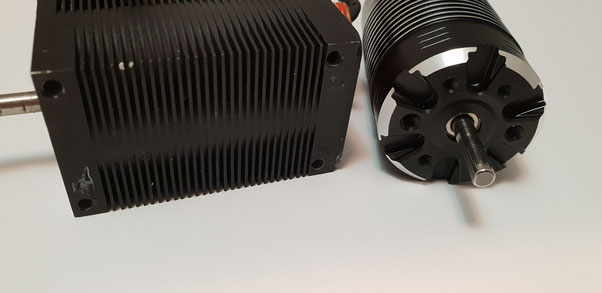
Die Variante von TTB (links im Bild) setzte eine Verschraubung über vier M4-Schrauben von der Unterseite voraus. Um verschiedene Untersetzungen des Getriebes zuzulassen und den Abstand des Motors zum Hauptzahnrad gewährleisten zu können, entschieden wir uns für Langlöcher auf der Unterseite mit versenkten Schrauben.
Für die Hobbywing-Antriebseinheit, welche die Variante mit rundem Gehäuse lieferte, legten wir die Vorderseite des Bocks so aus, dass wir für Welle und Ritzel die gleichen Ausfräsungen nutzen konnten, wie bei dem TTB-Motor. Da hier eine Verschraubung von der Stirnfläche des Motors erforderlich war, setzten wir auf der Vorderseite des Bocks ebenfalls Langlöcher.
Im Verlauf der Konstruktionsphase fiel auf, dass ein Bock der Mittelwelle sehr weit in den Bereich des Motorträgers hineinragte. Ausgemessen und im 3D-Modell vorgesehen, erstellten wir zunächst einen SLA-Druck des Bocks -diesen zeiteffizienten sowie niedrigschwelligen Weg wählen wir, um Konstruktionsfehlern vorzubeugen und mit einem geringen Kosten- und Zeitaufwand die Funktion zu überprüfen.
Fehler können auch uns passieren, sie fallen jedoch auf diese Weise nicht erst nach Fertigstellung des entsprechenden Frästeils auf, nachdem bereits hohe Materialkosten und viel Arbeitsaufwand entstanden sind. Abgesehen von einer kleinen Anpassung an den Verschraubungspunkten zwischen den Chassis und dem Motorbock, passten alle Varianten bei unserem ersten Versuch des Aneinanderfügens zusammen.
Im Vergleich SLA-Druck mit CNC Frästeil. Der 3D-Druck als optimale Lösung, um Bauraum und Design zu verifizieren.
Somit stand unser Konzept mit angepassten Verschraubungspunkten, mit dem wir in die Fertigung gehen konnten: Eine Bearbeitung von drei Seiten, welche wir auf unserer CAM gesteuerten MAHO MH 600 E ausführen konnten. Für das erste Musterteil beschränkte sich die Fräsbearbeitung auf einen Vormittag, da wir generell mit vorbereiteten Werkzeugwegen sehr kurze Zykluszeiten und damit eine optimale Ausnutzung der Maschinen gewährleisten können.